当Ultimaker遇上Print+ DIY耳机,格调和科技的冲撞or融合?
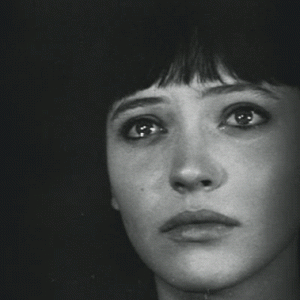
Jodie
今天同大家分享的是一个3D打印技术应用在电子产品头戴式耳机中非常成功的案例。Print+是一家荷兰公司,它推出的第一款产品——DIY耳机套装,在Kickstarter上大热,2天的时间便筹满资金。通过Ultimaker 3D打印耳机部件和Print+公司提供的DIY耳机套装,用户可以制作专属于自己的个性化定制耳机。
最新资讯
Ultimaker
UltiMaker:全新品牌形象,整合 Ultimaker 和 MakerBot
UltiMaker,一家全球领先的桌面3D打印公司,今天宣布在去年Ultimaker和MakerBot合并后重组其品牌。新的品牌形象体现了公司推动采用桌面3D打印解决方案的战略愿景,并引入了新的产品架构。- 威控睿博为你带来 UltiMaker 最新资讯!
2023-05-03
No Comments
Ultimaker
一文看懂 UltiMaker S7 的升级和改进
UltiMaker的首席技术官,揭示了该公司更新的旗舰FDM 3D打印机背后的创新。在这次访谈中,UltiMaker的首席技术官Miguel Calvo向我们介绍了UltiMaker S7的各项功能和改进,包括打印精度、印刷速度、可靠性、易用性等方面的改进,这些改进使得UltiMaker S7成为一个更加高效和可靠的3D打印机,适用于各种应用场景。
2023-04-24
No Comments
Blog
Ultimaker Cura 5.3 来了 – 新特性和新功能
让我们跟随Ultimaker的社区软件总监Arjen Dirks 一起看看新版本 Cura 的功能和修复改进。这些功能和修复改进能够为您的3D打印提供更大的灵活性、效率和质量,并附带了鳄鱼夹新特性。
2023-04-08
No Comments
Blog
全新Ultimaker Cura 5.0 究竟好在哪?
全新Ultimaker Cura 5.0将为您的打印带来怎样的非凡体验?请看Ultimaker Cura业务分析师Mariska Mass为您带来精彩揭秘!
2022-08-13
No Comments
Blog
Ultimaker 在线研讨会回放
2022年7月4日,Ultimaker举办了在线研讨会,向每个FFF 3D打印用户展示了如何使用Cura 5.0 获得更好的打印质量,以及解锁3D打印前所未有的新功能。如果您错过了本次会议或希望再次回顾内容,欢迎扫描下方海报二维码回看会议!
2022-07-08
No Comments
Cura
【Cura 下载】Ultimaker Cura 4.12 官方版本
Cura v 4.12 为用户带来了两大重要更新:”熨平“功能和“闪电填充”。“熨平“功能其实早在前几个版本中一直作为测试选项存在,新版本中成为了一个正式的功能供用户使用;“闪电填充”加入了一种全新的填充模式,能够大大减少打印时间。快来下载体验吧!
2021-11-12
No Comments